Facilities management can be a revolving door of continual repair and replacement. This generates extreme costs for businesses and is not always practical when equipment is needed day to day. The only way to stay on top of facilities maintenance is by keeping a close eye on the day to day running of buildings. Prevention is often much more effective (and affordable) than repair.
This is where thermal imaging comes in. So often thermal imaging is thought of as a tool for night vision and general surveillance. It actually has many practical uses, especially in terms of facilities management.
It’s a cost effective survey for facilities maintenance
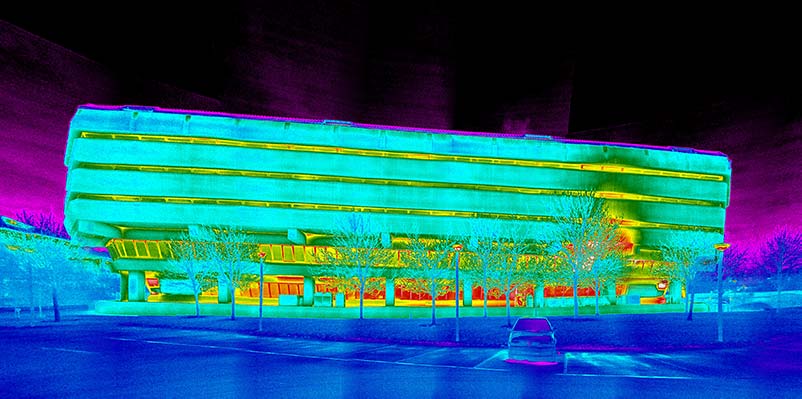
Thermal survey of a commercial building
Thermal imaging is a low cost way to maintain buildings and electrical equipment. It allows buildings to be surveyed easily, quickly and without destructive investigation. This in turn helps keep facilities maintenance budgets down.
As mentioned, one of the many benefits of thermal imaging surveys is that they are non-invasive. This means that investigation can be carried out without the need to damage and repair the building or machinery.
On top of that, thermal surveys can be done as part of predictive maintenance. This allows issues to be identified before they become visible to the naked eye.
It can show if your building is losing heat

Thermal survey of a rooftop
One of the most obvious ways to use thermal imaging to a great advantage is to check for heat loss. The specialist cameras scan the building and can identify if warm air is escaping. It can also show if there are any cold spots, small air gaps (which air tightness testing can struggle to find) and if there are issues with insulation.
Insulation gaps can be seen using the cameras from the outside. Whereas general interior scans can be more beneficial for checking for warm air escaping (because the air movement is reduced inside). A quick scan can tell if you are heating an area to no avail, and might also explain chilly members of staff!
It can quickly check equipment for facilities management
Much like humans, electronics and equipment generate heat. This heat can be picked up on a thermal imaging camera in the same way that other temperatures can.
Using a thermal camera on machinery allows those in charge of facilities management to easily check that equipment is performing as expected. It would be very easy to assess if there was a loose connection for example, as excessive amounts of heat would be being released. This is another example of smaller issues being able to be dealt with before they become big problems.
Often a machine won’t show signs of not working properly until it fully breaks down. Thermal imaging scans allow users to maintain it before that point, and help support the running of essential services.
It can help buildings and facilities stay more sustainable
Sustainability is a watchword for everyone in modern times, but it’s especially important for businesses. The pressure is on larger companies to be shown to be as ‘planet friendly’ as possible. Equally it can also benefit the business from practical standpoints.
As mentioned, thermal imaging can easily scan a building for things like heat loss and insulation gaps. The escaped heat means that the building’s heating system will be under increased demand to maintain a stable temperature. Even a few degrees means that more energy is required to supply the building and for the most part, that energy will still be from fossil fuels. Sustainability may not be at the forefront of facilities management, but it is becoming increasingly relevant in today’s world.
It can help with HVAC inspections
Heating, Ventilation and Air-Conditioning (HVAC) systems can be a complex and challenging part of facilities management. These systems allow for the monitoring of buildings, and can provide a wealth of information to a facilities manager. This means that it is crucial to keep these systems running effectively.
Thermal imaging can assist HVAC inspections by providing a clearer understanding of any heating and cooling issues relating to a building. Infrared cameras can also allow you to monitor electrical system faults, leaking ducts, insulation gaps, condensation leaks and mechanical problems.
It’s a great addition for fixed-wire testing
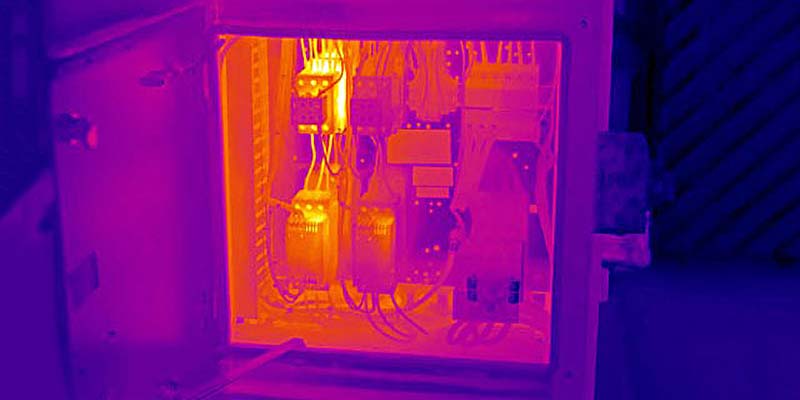
Live fixed-wire testing
Having safe running electrics can be the difference between an organisation being a well-oiled machine or not being able to run at all. If there is a failure in a building’s electrics that wasn’t spotted by facilities management, this could cause severe loss of income while it’s rectified.
A common cause of electrical issues is excessive current flow. This high flow will cause extra heat to be emitted. Thermal imaging is a very easy and non invasive way to see these issues before the damage is done. Something as simple as an overloaded circuit can also be seen with a thermal imaging camera and then dealt with. This stops the high power use, which would otherwise lead to increased costs.
It can identify roof leaks
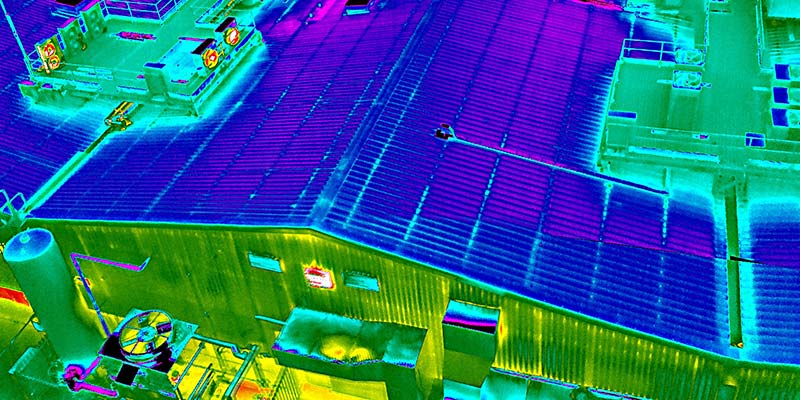
Drone thermal imaging survey
When attached to a drone, thermal cameras can be used to identify areas where too much water is collecting. This is something that is much more accessible than having to cause damage to the roof with a more physical inspection.
This can be a huge benefit to commercial business and facilities management. Roof replacement is an exorbitant cost. A single leak can cause a lot of damage within a building itself.
iRed® is here to assist you with your building management needs. We offer affordable thermal imaging surveys, allowing you to see where there are issues with heat or electrics. Don’t let small issues become big problems unnecessarily. Let us help you reduce your annual bills, whilst making facilities maintenance a much easier task.
As the UK’s leading provider of thermal imaging solutions, you can put your trust in us.