ELECTRICAL THERMAL IMAGING
Non-contact thermal imaging surveys with zero downtime.
We provide live fixed-wire testing for panels, distribution boards and connections – avoiding the need for costly down-time.
LEARN MORE
Find faults and reduce risk with electrical thermal imaging inspections
UK’S LEADING PROVIDER OF THERMAL IMAGING SURVEYS
iRed® is the largest independent thermal imaging consultancy in the UK. As the preferred supplier for NHBC and leading home-builders nationwide, you can trust that your building is in safe hands with us.
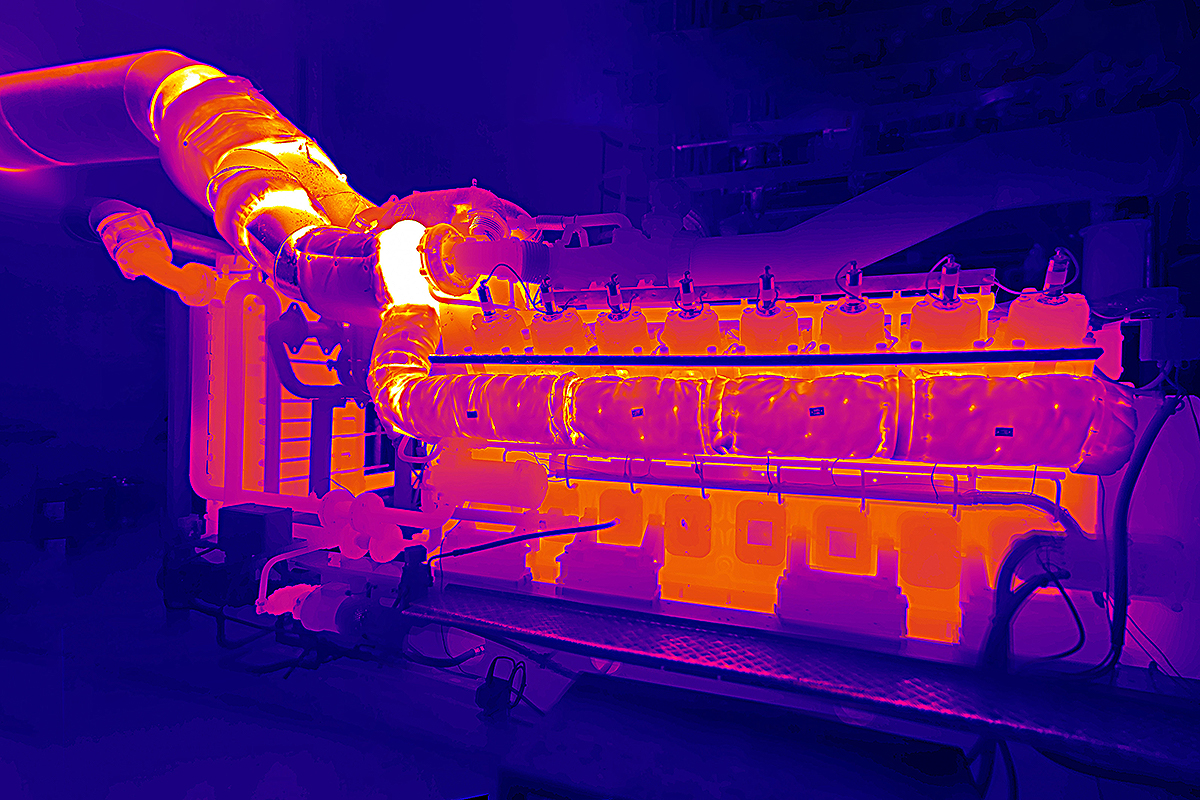
FAULT-FINDING
Find out where you’re exposed – without interrupting business
Reduction or failure within electrical infrastructures can have far reaching consequences creating unnecessary downtime and long term financial impact.
Our friendly team of experts use thermal imaging cameras to undertake live, fixed-wire testing for panels, distribution boards and connections – avoiding the need for costly down-time.
FACILITIES MANAGEMENT
Reduce energy costs by detecting and predicting electrical faults
By detecting faults and poor connections early, electrical thermal imaging can avoid costly down-time and expensive repairs.
Our surveys also include a repeatable point-inspection, analysis and comparison – providing a cost-effective solution for annual maintenance and fire risk assessments.
Discover your riskiest assets and find out where you’re exposed – without interrupting business
Non-contact thermal imaging surveys for routine maintenance and fault-finding.
“iRed’s professionalism is apparent in both their approach to the client on site and to the report production aspect which is delivered in an easy to understand and visually pleasing format.”
“iRed have proved themselves to be very flexible in fitting in with our policies and procedures, the engineers have been very efficient and I have been impressed with the final presentation of the results.”
“As a business, iRed have proved their worth time and time again. The professionalism of the office staff, united with engineer know-how of thermographic engineers is a formidable team.”
Certified Inspectors
We’re proud to have the largest team of certified category 2/3 thermal inspectors in the UK.
Nationwide Surveys
We’re proud to be trusted by over 2,500 customers across a broad range of industries nationwide.
Latest Technology
In partnership with FLIR and DJI, we only use the very latest commercial inspection tools and sensors.
3 SIMPLE STEPS FOR BOOKING YOUR SURVEY
Questions? Call our team on 01243 370 296 or email [email protected]
We’re approved and accredited

We’re proud to maintain a number of accreditations, certifications, awards and affiliations from national and global organisations.
Frequently Asked Questions